Robotics, AI & ML
Remote Handling & Robotics Technology



In addition to the domestic developments, IPR as part of international collaboration has completed and delivered remote handling task agreements with ITER-IO, France and JET, UK
Artificial Intelligence Software for Fast Automated Screening of Chest Ailments (such as TB) using Chest X- Ray Images, in collaboration with ICMR headquarters, Delhi. -https://tb.ai.icmr.org.in/ai4tb/





DeepCXR
Institute of Plasma Research developed AI tool for detection of TB and other lung disease using Chest X-ray, was tested on limited data set and therefore the entire range of variables have not been covered.
MOU signed & training of tool initiated on the data of culture confirmed X-rays from previous surveys which includes data from four zones of India.
At present tools are in advanced stage of testing with numerous images from various sources. This work is being carried out in collaboration with Civil Hospital, Ahmedabad, ICMR, head quarter Delhi, NIRT, Chennai and other participating institutes/medical colleges in India. The software has the capability of processing more than 250 images in 30 mins.
A central website has been developed at ICMR Delhi https://tb.ai.icmr.org.in/ai4tb/
A pre processing software was developed by IPR and training was given to all participant institutes .
For our software DeepCXR we need digital CXR(chest x-ray). For this purpose a prototype of digitizer of chest X-rays was developed and tested.
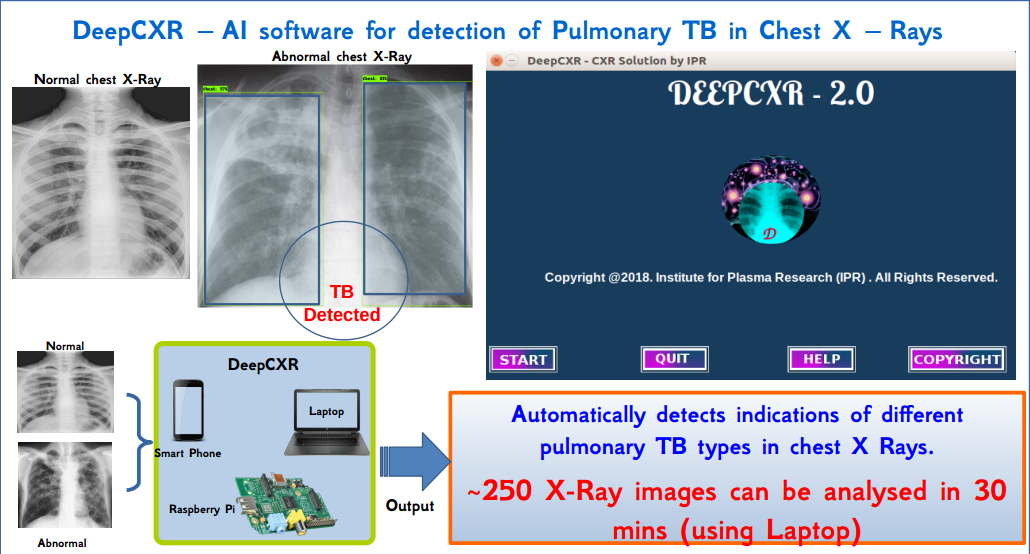
AIBacilli
This is another AI software developed at IPR for automated detection of single/multiple mycobacillus in sputum smear test. This AI based Software uses AI based technique of Object Detection. Software development together with the relevent Hardware automation is being carried out to simplify the current practice. The work is being carried out in collaboration with Civil Hospital, Ahmedabad.
The softwares are capable of running on CPU/GPU/ARM devices.
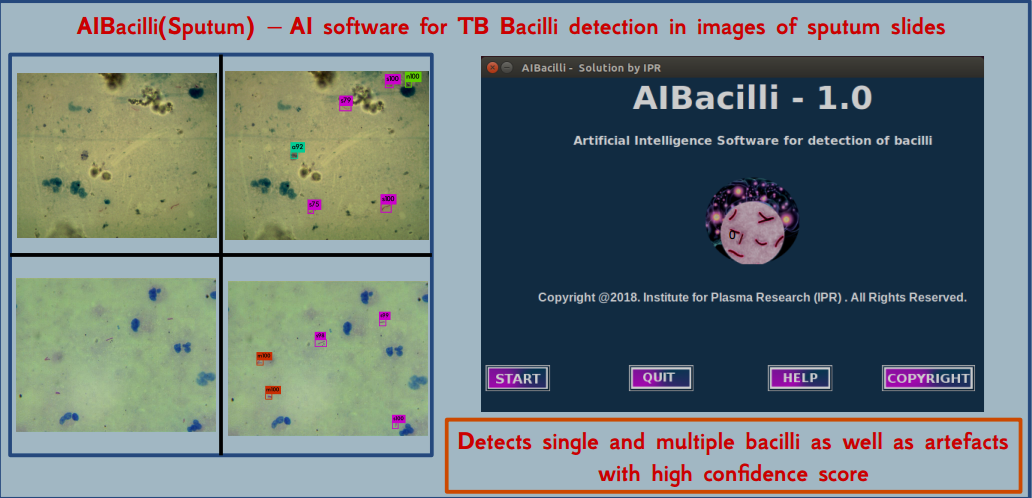
AI tools on the top of existing security systems are designed, developed and deployed for 24 x 7 monitoring of critical areas/lab spaces etc. GUI interface, data storage, network connectivity forms the part of the system. We have trained,tested and validated a CNN model which determines the object of interest (human) in live CCTV frames.
Blockchain technology for data sharing/authentication/Validation
Blockchain Technology: Web 3.0 based advanced encryption technologies are integrated with current software to leverage the benefits of decentralization. The software is designed to interact with public blockchain nodes, stores the encrypted values in block of defined pre-defined contract to be retrieved at later date. The software has numerous applications like govt data repository, certificates, digital health records etc.
Recent Publications
1 A. Abhishek et al, Real Time Close Circuit Television: Artificial Intelligence Monitoring Solution, Technical Report-617, Feb 2021
2 A. Abhishek et al System and Method for Screening Chest X-Ray Image for Diagnosis, – Indian Patent App. No. 201921016615
3 Manika Sharma, H. Hemani et al , Towards finding Vocal signatures of Covid-19 in cough Sounds –IPR/RR-1253/2021
4 SC A Vaid et al., Emerging Advanced Technologies Developed by IPR for Bio Medical Applications - A Review, Neurol India 68 (1), 26-34, 2020
Conference presentations :
An Artificial Intelligence based Solution for SST1 Tokamak building monitoring, Agraj Abhishek et al, Poster presented in PSSI 2021
Image processing and its application in Tokamak
Introduction Visible image acquisition is one of the activities during Plasma experiments to diagnose Tokamak Plasma. Due to the presence of strong magnetic fields in and around Tokamak, the camera cannot be directly kept inside the Tokamak. For imaging purpose where camera can’t be used directly, optical fiber bundle is used with camera to capture image. The image captured using optical fibre bundle has some noise, which is referred as Honeycomb structure. Software package developed for removal of honeycomb structure. The executable software package is capable to read from USB/IP camera or from stored video file.
A prototype for image processing based feedback as required for experimental setups is also being developed and tested.
![]() Fig: Image captured using wound image bundle (noise can be seen in black stripes referred as honeycomb structure )
| ![]() Fig:Digitally processed to provide clear image
|
Image processing of plasma images for boundary extraction (from SST-1 imaging diagnostic)
Digitally processed to provide clear image with plasma boundary extraction
captured using wound image bundle (noise can be seen in black stripes referred as honeycomb structure )
Remote Handling & Robotics Technology
![]() IPR Virtual Reality Facility
| ![]() IVIS SYSTEM
|
Remote Handling is often described as the synergistic combination of technology and engineering management systems to enable operators to safely, reliably and repeatedly perform manipulation of items without being in personal contact.
The scope of this project is to build a versatile Remote Handling System for challenging environments. The major objectives are design and development of dexterous articulated robotic arms, dual arm manipulators, hyper redundant inspection systems, haptic arms, mobile robots etc. capable to carry out inspection and maintenance activities in challenging environments such as presence of ultra high vacuum, high temperature, narrow spaces, magnetic fields, etc.
The developments also include establishment of advanced Virtual Reality (VR) CAVE facility and development of interactive VR applications catering to operator training, kinematic testing, assembly & maintenance, interface studies, safety management, operation sequences, monitoring and control of RH operations.
The development of the technologies and systems are being carried out in a parallel and interrelated mode with support of external agencies and institutions.
Recent developments:
1. Fully Immersive Virtual Reality (VR) CAVE Facility - AABHAS







2. UHV compatible articulated In-Vessel Inspection System (IVIS)





![]() IVIS System with a toroidal chamber
![]() Overall systematic of IVIS System
|
3. Hyper Redundant Inspection System (HyRIS)




4. Indigenous development of Haptic master arm for tele-manipulation




![]() ![]() IPR Virtual Reality Facility
|
![]() IVIS SYSTEM DEMO
|
![]() VR application for Operator Training
|
![]() Schematic of the 6 Joints Hyper redundant inspection system
|
![]() VR based demonstration of automated waste handling in pyrolysis system
|
![]() Dual Arm Manipulator
|
![]() IVIS Deployment in SST-1
|
Achievements
1) Successfully Established of 3 sided fully immersive Cave Automatic Virtual Environment (CAVE) VR facility at IPR
2) In-Vessel Inspection (IVIS) System is First UHV compatible 06 DOF articulated arm in India.
3) A VR based control system for monitoring and controlling articulated robotic inspection arm (50 kg payload at 2.2m reach) has been developed and tested successfully
In addition to the domestic developments, IPR as part of international collaboration has completed and delivered remote handling task agreements with ITER-IO, France and JET, UK
Recent Publications







- Artificial Intelligence
- Image Processing
- Remote Handling & Robotics Technology